Quality Control Process
Explore the essentials of the Quality Control Process to ensure product excellence, consistency, and customer satisfaction
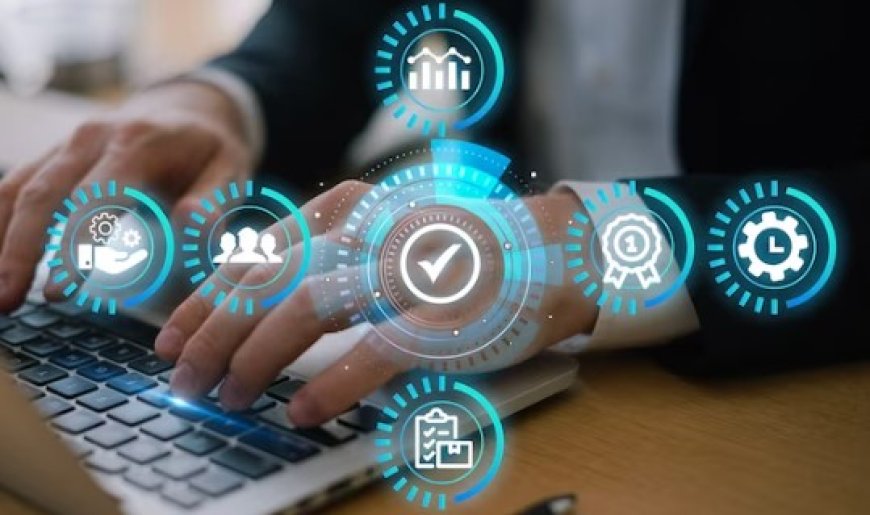
Quality control plays a pivotal role in ensuring products meet established standards and fulfill customer expectations. It involves systematic processes designed to measure and maintain the quality of products at every stage of production, from sourcing raw materials to the final delivery. This vigilance not only safeguards the consistency of product performance and safety but also significantly contributes to customer satisfaction. By identifying and rectifying defects before products reach the market, businesses can reduce returns and complaints, enhance their reputation, and foster customer loyalty. In essence, effective quality control is fundamental in maintaining a competitive edge, ensuring compliance with regulations, and building trust with consumers.
Overview of the current state of quality control in industries
-
In manufacturing, quality control is pivotal for ensuring products meet safety and customer standards, involving checks at various production stages.
-
Software development employs quality control to detect bugs and ensure software meets user requirements and functions as intended.
-
Service industries use quality control to maintain service excellence, evaluating customer feedback and service delivery consistency.
Quality control processes have become an integral component across various industries, serving as the backbone for maintaining product integrity and reliability. These processes are not just about adhering to compliance standards but are fundamental to delivering value to customers. The general acceptance and reliance on quality control are rooted in its undeniable impact on product quality and safety. In today's competitive market, organizations recognize that consistent quality is key to customer satisfaction and loyalty. This recognition has led to the widespread adoption of systematic quality control measures, designed to ensure that products and services not only meet but exceed customer expectations. As industries evolve and consumer demands become more sophisticated, the role of quality control in sustaining business success and reputation continues to expand, making it an indispensable part of operational strategy.
The Hurdles of Quality Control
Implementing effective quality control processes is a critical challenge for many organizations, fraught with obstacles that can hinder the achievement of high-quality standards. These challenges often stem from a variety of sources, complicating efforts to maintain consistency and excellence in products or services. Understanding these hurdles is the first step toward overcoming them.
Resource Constraints: One of the primary barriers is the limitation of resources. This can manifest as a lack of financial investment for quality control technologies or insufficient manpower to cover all necessary quality checks. When resources are stretched thin, corners may be cut, and the thoroughness of quality control processes could suffer.
Technological Limitations: Despite the advances in technology, many organizations still grapple with outdated or inadequate quality control systems that fail to catch defects or issues efficiently. The reluctance or inability to adopt newer, more effective technologies can leave companies lagging behind, unable to identify or address quality issues before they reach the customer.
Human Error: Even with the best processes and technologies in place, the human element remains a variable that can introduce errors. Misinterpretation of data, oversight, or simple mistakes made during quality control checks can lead to inconsistencies and defects in the final product. Training and vigilance can mitigate this, but human error remains a persistent challenge.
Evolving Consumer Expectations: In today's fast-paced market, consumer expectations are constantly evolving. What was considered high quality a year ago may now be deemed average or inadequate. This shifting landscape makes it challenging for organizations to keep up with what quality means to their customers, necessitating a flexible and responsive approach to quality control that can adapt to changing standards.
Together, these challenges paint a complex picture for organizations striving to implement effective quality control processes. The path forward involves not just recognizing these obstacles but actively seeking innovative solutions to navigate them.
How can organizations refine their quality control processes to effectively navigate these challenges and not only meet but surpass industry standards and customer expectations?
Enhancing quality control processes is crucial for organizations aiming to maintain high standards of product and service delivery. By following a step-by-step guide, organizations can address gaps in their current systems, leverage technology for efficiency, and ultimately exceed customer expectations. Here's an expanded view of each step in the guide:
1. Comprehensive Evaluation:
-
Start by conducting a thorough audit of your existing quality control (QC) processes. This involves reviewing all current procedures, standards, and outcomes to identify inconsistencies, failures, or areas lacking efficiency.
-
Utilize both quantitative data (defect rates, inspection results) and qualitative feedback (from QC personnel, operational staff) for a holistic understanding.
-
The goal is to pinpoint weaknesses that could lead to product defects, delays, or customer dissatisfaction.
2. Adopting Technology:
-
Explore and implement modern technologies designed to enhance quality control. This could range from automated inspection systems and AI-driven defect detection to software solutions for better data management and analytics.
-
For example, adopting a Manufacturing Execution System (MES) can provide real-time insights into production processes, identifying issues as they happen.
-
The integration of such technologies not only improves accuracy and speed but also reduces the human error factor in quality control.
3. Training and Development:
-
Ensuring that all employees, especially those directly involved in QC processes, are well-trained and knowledgeable about the latest quality standards and methodologies.
-
Develop a continuous learning culture where training is not a one-time event but an ongoing process. This includes regular updates on industry best practices and refresher courses.
-
Empower employees by involving them in quality improvement initiatives, encouraging them to suggest improvements based on their day-to-day experiences.
4. Continuous Improvement:
-
Adopt a philosophy of continuous improvement, such as Kaizen, which focuses on making small, incremental changes that lead to major improvements over time.
-
Implement a feedback loop where information from QC checks is used to constantly refine processes. This includes regular review meetings to discuss what's working, what isn't, and how processes can be optimized.
-
Use Key Performance Indicators (KPIs) to measure the effectiveness of quality control processes and set benchmarks for improvement.
5. Customer Feedback:
-
Actively seek out and incorporate customer feedback into the quality control process. Understanding customer expectations and experiences can provide critical insights into where improvements are needed.
-
Implement mechanisms for easy feedback collection, such as surveys, focus groups, or direct communication channels.
-
Treat customer feedback as a valuable resource for continuous product and service improvement. Regularly review feedback trends and address any recurring issues.
By systematically addressing each of these steps, organizations can create a robust quality control process that not only meets but exceeds industry standards and customer expectations. The key is a commitment to ongoing evaluation, adaptation, and improvement, ensuring that quality remains at the forefront of operations.
In this evolving marketplace, the continuous evolution and enhancement of quality control processes are not just beneficial but essential for staying competitive and upholding high-quality standards. The dynamic nature of consumer expectations, technological advancements, and regulatory environments necessitates a proactive approach to quality control. This approach not only safeguards the integrity and reputation of your products and services but also ensures they resonate with your target audience and meet stringent industry benchmarks.
The steps outlined provide a comprehensive framework for organizations looking to refine their quality control mechanisms. By conducting a comprehensive evaluation, embracing technology, investing in training and development, fostering a culture of continuous improvement, and integrating customer feedback, businesses can significantly elevate their quality control efforts. These strategies are designed to address common challenges, capitalize on new opportunities, and align quality control processes with the ever-changing landscape of customer expectations and industry standards.
Regardless of size or sector, to periodically reassess their quality control strategies against the guidelines provided. This not only helps in identifying areas for improvement but also in ensuring that quality control processes remain robust, responsive, and relevant. The commitment to continuous quality enhancement is a commitment to your customers, your brand, and your future success. Let these steps guide you in your quest for excellence, driving improvements that lead to superior products, satisfied customers, and a formidable market presence.